Basics and Advanced Techniques of Aluminum Laser Cutting and Engraving
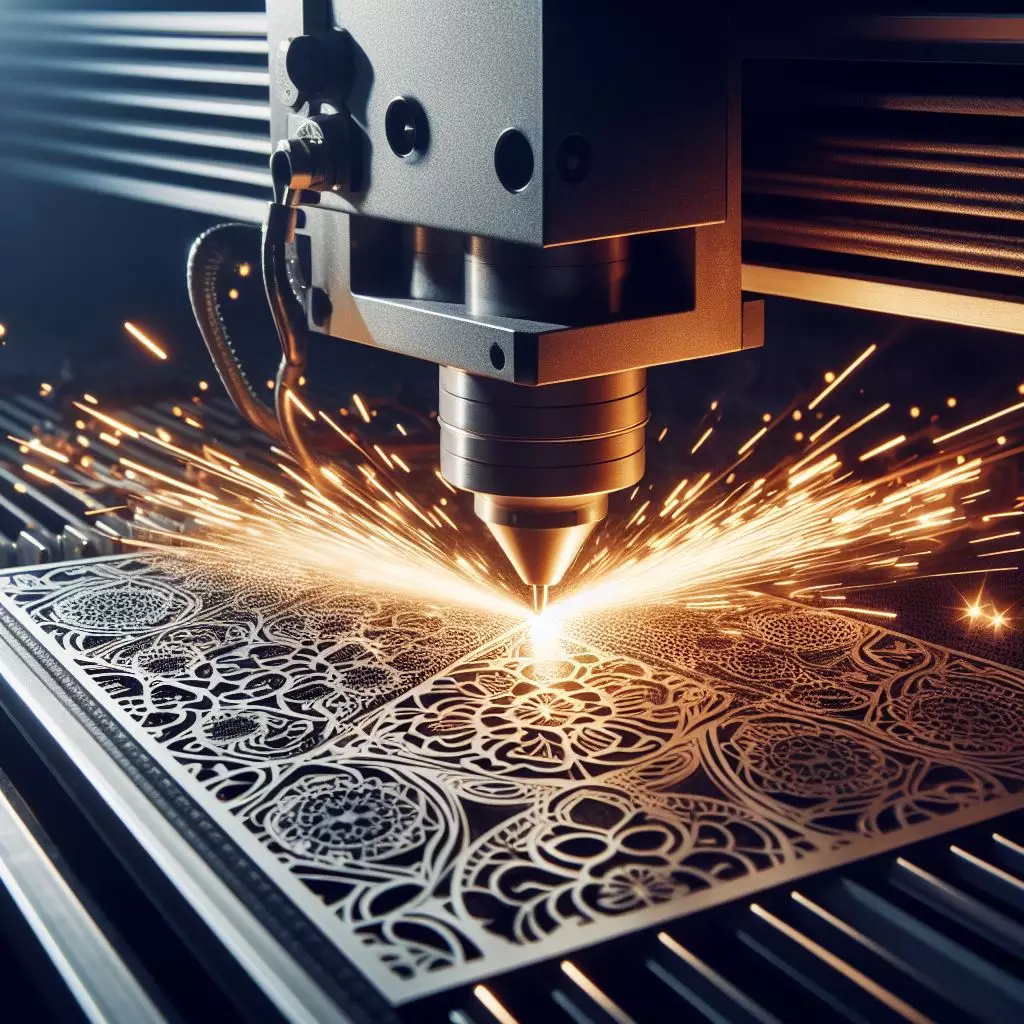
Aluminum laser engraving is a refined and captivating method for applying precise and intricate designs to metal. Compared to other engraving techniques, laser engraving offers several advantages such as higher precision and faster completion times. However, achieving the best results in aluminum laser engraving is crucially dependent on selecting the right laser and meticulously preparing the aluminum material.
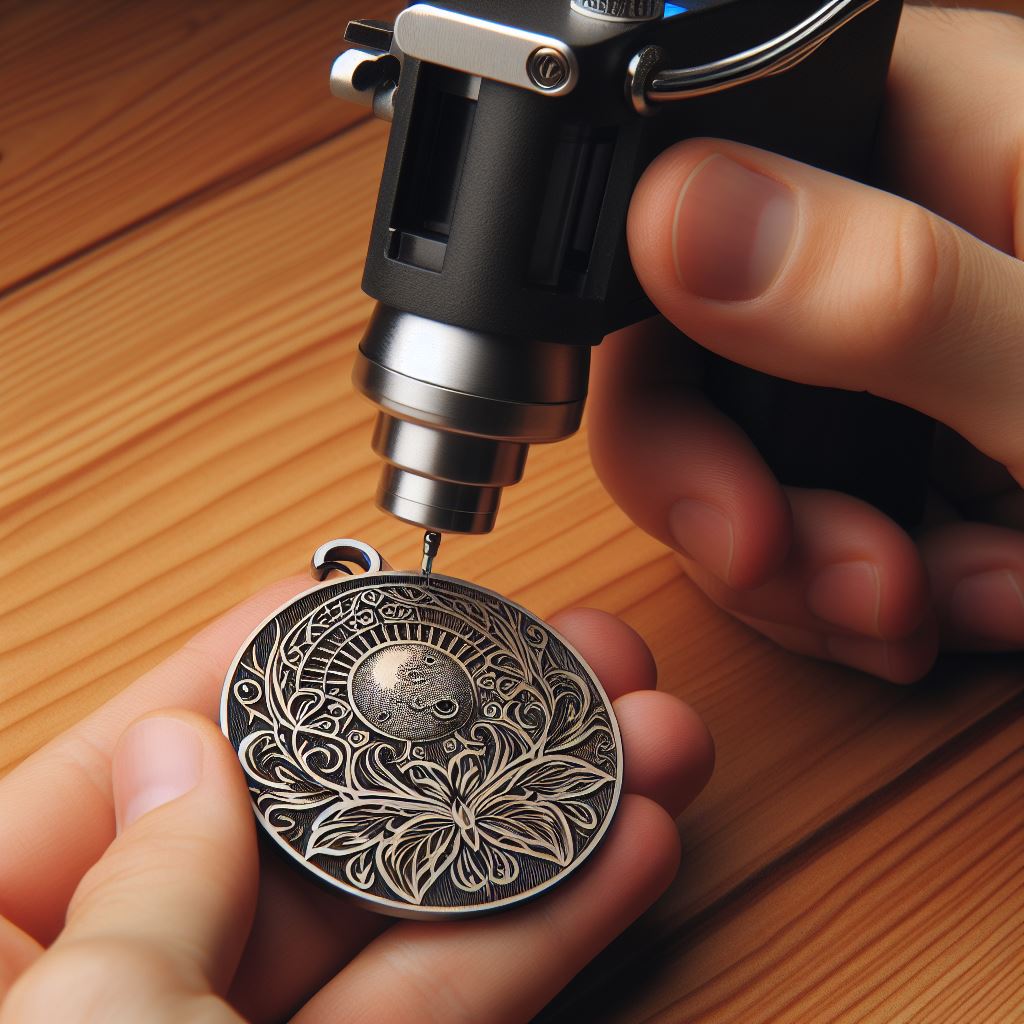
Advantages of Laser Engraving Over Other Processes
Laser engraving showcases numerous benefits when processing aluminum, making it an ideal choice. One of the most significant advantages is the precision and intricacy of material engraving. Laser technology can achieve extremely fine details with high quality on aluminum.
Additionally, the process is rapid and efficient—even for mass production. Compared to other methods like milling or stamping, laser engraving does not produce any burrs or debris, ensuring a clean and smooth finish.
Another major advantage is its flexibility: Thanks to advanced software technology, nearly all designs are achievable—from fonts and logos to complex patterns and textures. In summary, if you seek precise, fast, and flexible aluminum processing, laser engraving is your best option.
Choosing the Right Laser for Aluminum Engraving
When selecting a laser suitable for aluminum engraving, several factors need consideration. First, you need to determine the type of engraving—is it merely surface engraving, or is deeper material cutting required? The size and shape of the object to be engraved also play a role in choosing the laser.
For instance, CO2 lasers are more suitable for large surface areas, while fiber lasers can produce precise lines and etching on smaller objects. Another important consideration is the power of the laser; the higher the wattage, the faster the operation.
However, cost and operational expenses must also be considered, as more powerful lasers are more expensive and require more energy. Overall, with the right laser, you can perform fine engravings and markings on aluminum in various ways—from company logos to personalized gifts.
Basics of Aluminum Laser Cutting
Laser cutting uses a highly focused laser beam to cut materials. Using a laser cutter on aluminum—a metal known for its lightness and strength—enables high precision and speed in cutting, which is particularly advantageous in industries such as automotive, aerospace, and electronic and mechanical engineering components.
Advantages of Aluminum Laser Cutting
- Precision: Laser cutting can achieve complex contours and fine details that other cutting methods cannot match.
- Efficiency: Laser cutting offers quick cutting speeds, reducing the need for tool changes and significantly shortening production times.
- Flexibility: Laser cutters can handle various thicknesses and types of aluminum alloys without needing major machine adjustments.
- Cleanliness: Laser-cut edges are clean and burr-free, greatly reducing the need for post-processing cleanup and finishing.
Technical Challenges in Aluminum Laser Cutting and Engraving
Despite the many advantages, aluminum laser cutting and engraving present several technical challenges in practice:
Reflectivity: Aluminum’s high reflectivity can damage laser equipment, necessitating special settings and parameter adjustments to ensure safe and effective cutting.
Thermal Conductivity: Aluminum’s high thermal conductivity means heat distributes quickly during laser cutting, which can affect the quality of the cut, especially in detail work.
Cutting Gas: When laser cutting aluminum, it is often necessary to use cutting gases such as nitrogen or argon to prevent oxidation and achieve clearer cutting edges.
Optimizing Aluminum Laser Cutting Processes
To overcome these challenges and enhance the overall effectiveness of aluminum laser cutting, here are some optimization strategies:
- Equipment Selection: Using laser cutting machines specifically designed for aluminum or other highly reflective materials, which usually feature more advanced laser sources and control systems, can improve efficiency and quality.
- Parameter Adjustments: Fine-tuning the laser’s power, speed, and focal distance to suit the characteristics of aluminum is crucial for maximizing cutting efficiency and minimizing heat-affected zones.
- Software Applications: Modern CAD/CAM software aids in precise cutting path planning, reducing errors and enhancing repeatability.
- Technical Training: Ensuring that operators possess the necessary technical knowledge and practical experience to effectively manage the laser cutting process and address technical issues promptly.
By implementing these advanced strategies and techniques, aluminum laser cutting and engraving not only meet high efficiency and precision production requirements but also promote more innovative applications in the design and manufacturing industries.