Comparison Between Laser Cutting Machine and Traditional Stamping Machine
Fiber laser cutter is an alternative to traditional stamping technology. The CNC punch press is a metal sheet forming machine tool. In traditional technology, it mainly plays a role in the “blanking” link in metal sheet processing. As the laser cutting process matures, it is inevitable that laser equipment will replace CNC punch machines, but punch machines will not completely disappear. CNC punch machines still play a vital role in some functional links that cannot be replaced by lasers. At this stage, my country’s laser cutting has basically completed the rapid replacement of traditional stamping technology, and the demand for laser cutting equipment and CNC punch machines maintains a relative dynamic balance.
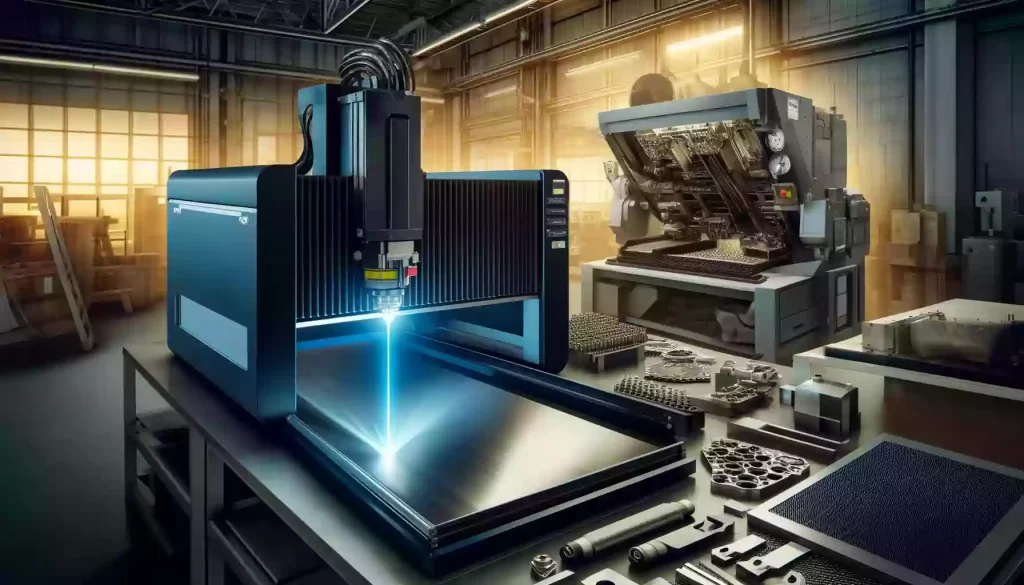
Ⅰ.Working Principle
1.Laser cutting machines’ working principle
Fiber laser cutter use high-power laser beams to focus on the surface of the material and cut by melting or vaporizing the material. The laser beam is precisely controlled by the optical system and CNC system, enabling cutting and engraving of complex patterns.
2.Traditional stamping machines’ working principle
Traditional stamping machines use mechanical pressure to bring the mold into contact with the material, causing the material to deform or break to achieve the purpose of cutting. Stamping machines rely on the shape and accuracy of the mold, so it takes a certain amount of time and cost to replace the mold.
Ⅱ.Cutting Speed
Laser cutting is fast. The cutting speed of laser cutting equipment is more than 10 times that of CNC stamping machine tools. Compared with traditional cutting methods, the advantages of laser cutting mainly include fast cutting speed and high processing accuracy. Specifically, it includes: high precision, fast speed, narrow cutting slit, small heat-affected zone, and smooth cutting surface.
Ⅲ.Cutting Quality and Precision
1.Laser cutting machine has high cutting quality and precision
Laser cutting quality is high. The main reason why laser cutting causes very little damage to materials is that it is a non-contact processing technology, which does not require secondary processing, and its accuracy is better than that of stamping technology.
2.Traditional matal cutting machine lacks of high cutting quality and precision
As a traditional metal cutting method, CNC punching machine has a relatively large restriction, which is the loss of material. At the same time, from the perspective of cutting effect, it is not as good as laser cutting, which usually requires secondary processing. However, there is still a lack of accuracy.
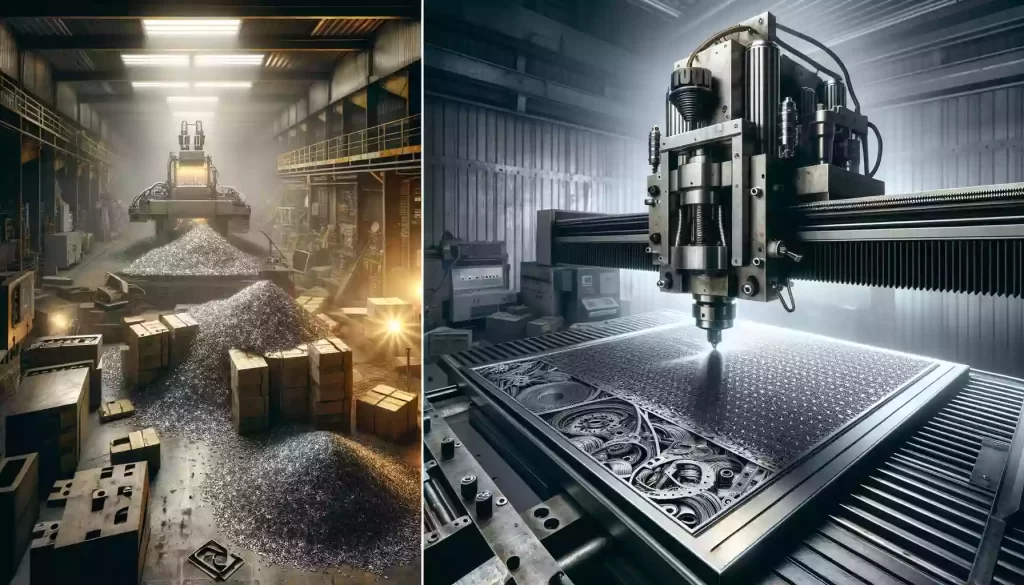
Ⅳ.Productivity
1.Laser cutting machines good at processing small batches and high-variety products.
Laser cutting machines have significant advantages when processing small batches and high-variety products. Since there is no need to change the mold, you only need to adjust the CNC program to switch products, saving a lot of time and cost. For complex patterns, laser cutting machines are faster and more efficient.
2.Conventional stamping machines good at processing high-volume production
Conventional stamping machines excel in high-volume production. Multiple parts can be processed in one stamping operation, which is very efficient. However, the design and manufacturing costs of molds are high, and mold replacement requires a certain amount of time, so it is not suitable for production environments where products are frequently changed.
Ⅴ.Application Scope
1.Laser cutting machines good at processing complex and demanding parts
Laser cutting machines are widely used in sheet metal processing, advertising signs, electronic appliances, automobile manufacturing and other fields. Its high precision and flexibility give it clear advantages when processing complex and demanding parts. In addition, laser cutting machines can also be used for processing non-metallic materials, such as wood, plastics, ceramics, etc.
2.Traditional stamping machines good at processing simple parts
Traditional stamping machines are mainly used in mass production fields such as automobiles, home appliances, and electronics. Its high efficiency and low processing cost are suitable for the production of standardized and large-volume parts. Stamping machines excel at processing thick sheet metal and harder materials, but are not as good as laser cutters when handling complex shapes and low-volume production.
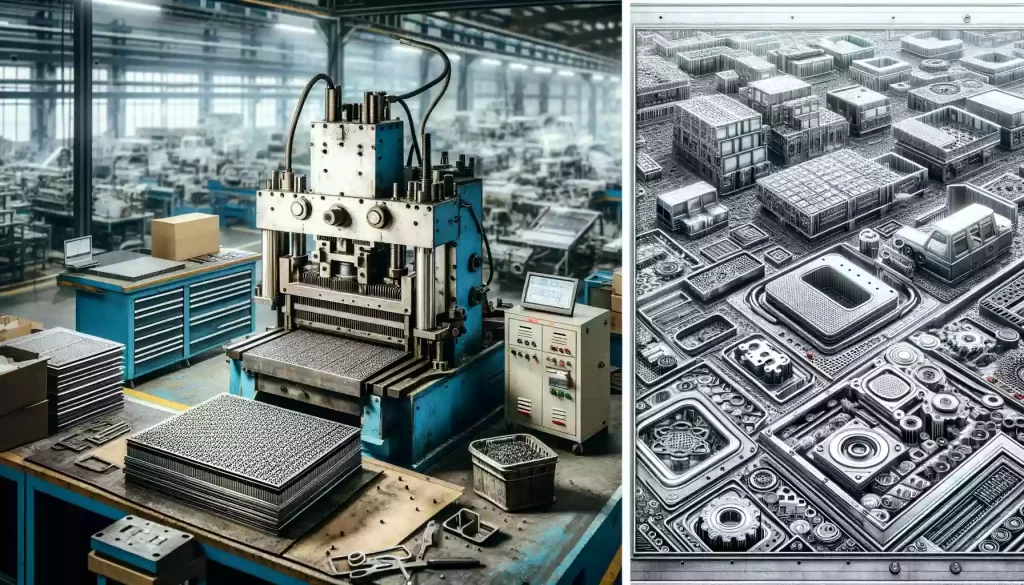
Ⅵ.Environmental Protection and Safety
1.Laser cutting machines is environmental friendly and needs safety equipment
Laser cutting machines perform better in terms of environmental protection and safety. The laser cutting process does not produce a lot of noise and vibration, and the working environment is relatively quiet. In addition, the laser cutting process produces less waste and causes less environmental pollution. However, it should be noted that the laser cutting machine will produce smoke during the cutting process and needs to be equipped with good ventilation and dust removal systems.
2.Traditional stamping machines results environmental pollution
Traditional stamping machines will produce greater noise and vibration, which will have a certain impact on the health of operators and the working environment. In addition, a lot of waste is generated during the stamping process, and effective waste treatment is required to prevent environmental pollution.
Final Thoughts
To sum up, laser cutting machines and traditional stamping machines each have their own advantages and disadvantages. With its high precision, flexibility and environmental protection performance, laser cutting machines perform well in processing small batches, multiple varieties and high-demand parts; traditional stamping machines have significant advantages in large-volume, standardized production. In actual production, enterprises should reasonably select appropriate processing equipment based on specific production needs and product characteristics to achieve the optimal balance between production efficiency and product quality.