Comparisons Between Laser Cutting Machine, Wire Cutting Machine and Plasma Cutting Machine
Fiber laser cutter, wire cutting machine and plasma cutting machine are three common cutting technologies in modern manufacturing industry. They each have their own characteristics and application fields. This blog will make a detailed comparison between them in terms of features and applications:
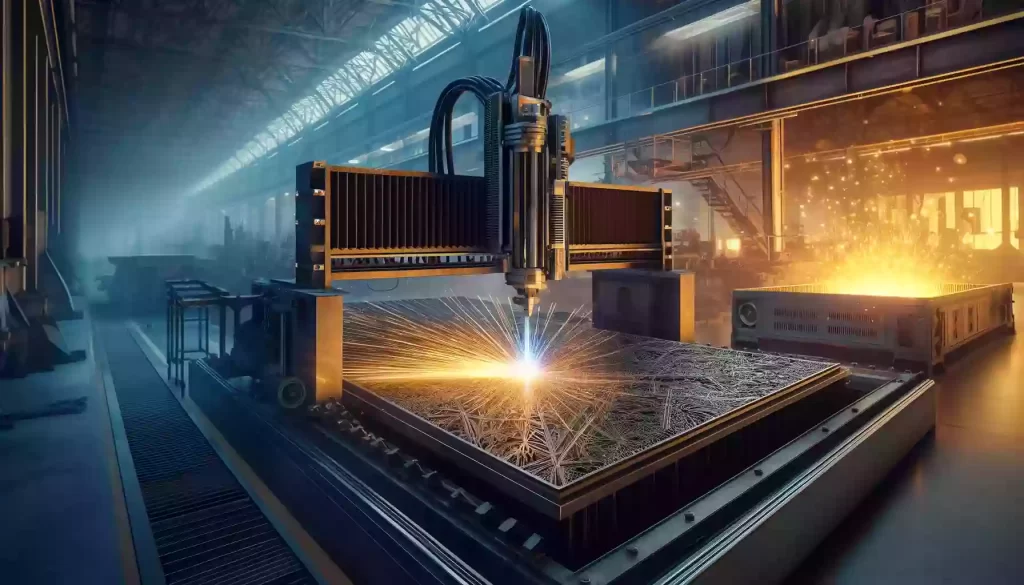
Ⅰ. Fiber Laser Cutting Machine
Fiber laser cutting machine is a device that uses a high-energy-density laser beam as a cutting tool and irradiates the material with the focused laser beam to quickly heat, melt, evaporate or reach the burning point, thereby achieving cutting. The technology has the characteristics of high precision, fast cutting speed, smooth incision and small heat-affected zone.
1.Characteristics:
High precision:
Laser cutting machines can achieve millimeter-level or even higher-precision cutting, and are suitable for precision processing.
Applicable to a wide range of materials:
It can cut metals, non-metals, ceramics, glass and other materials.
Flexible operation:
Laser cutting does not require contact with the material and can achieve cutting of any shape.
2.Application restrictions:
Higher cost:
The purchase and operating costs of laser cutting machines are relatively high.
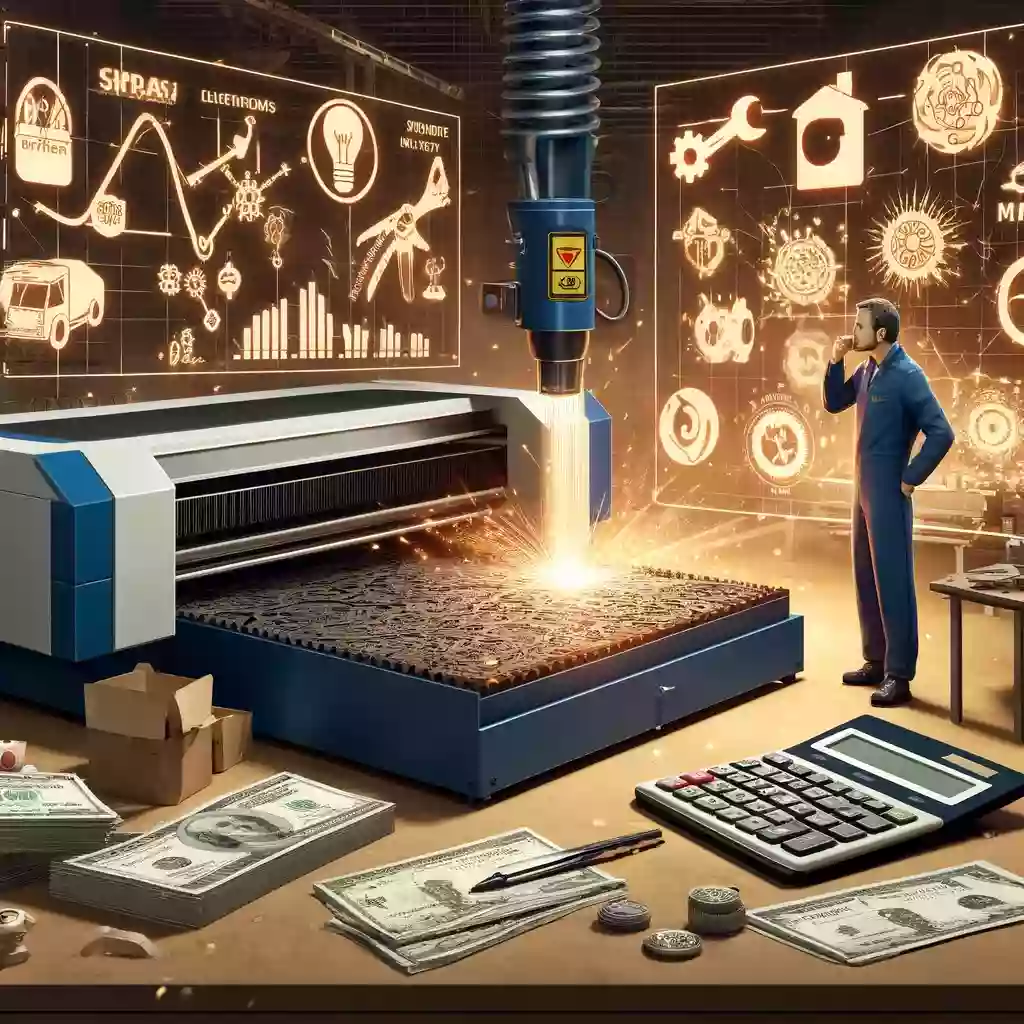
Thickness limitation:
For materials exceeding a certain thickness, the efficiency and quality of laser cutting will decrease.
Ⅱ. Wire cutting machine
Wire cutting machine is a device that uses a continuously moving thin metal wire (usually molybdenum wire or copper wire) as an electrode to generate a pulse discharge between the electrode and the workpiece, and relies on the principle of discharge ablation to perform cutting. These machines are particularly suitable for processing hard and brittle materials such as carbide and quartz and parts with complex shapes.
1.Characteristics
Fine processing:
Wire cutting machines can process tiny holes and complex contours.
Forceless cutting:
no force is exerted on the material during the cutting process, and is suitable for brittle materials.
2.Application restrictions:
Slow processing speed:
Compared with laser cutting and plasma cutting, the processing speed of wire cutting is slow.
Material limitations:
Mainly suitable for conductive materials, but not for non-conductive materials.
Ⅲ. Plasma cutting machine
A plasma cutting machine is a device that cuts conductive materials through a high-temperature plasma arc between an electrode and a workpiece. It forms a plasma state by heating gas to extremely high temperatures, melting metal at high temperatures and blowing away the molten metal with the help of high-speed plasma flow.
1.Characteristics
Large cutting thickness:
Plasma cutting can handle thicker metal sheets, especially for materials such as carbon steel, stainless steel and aluminum.
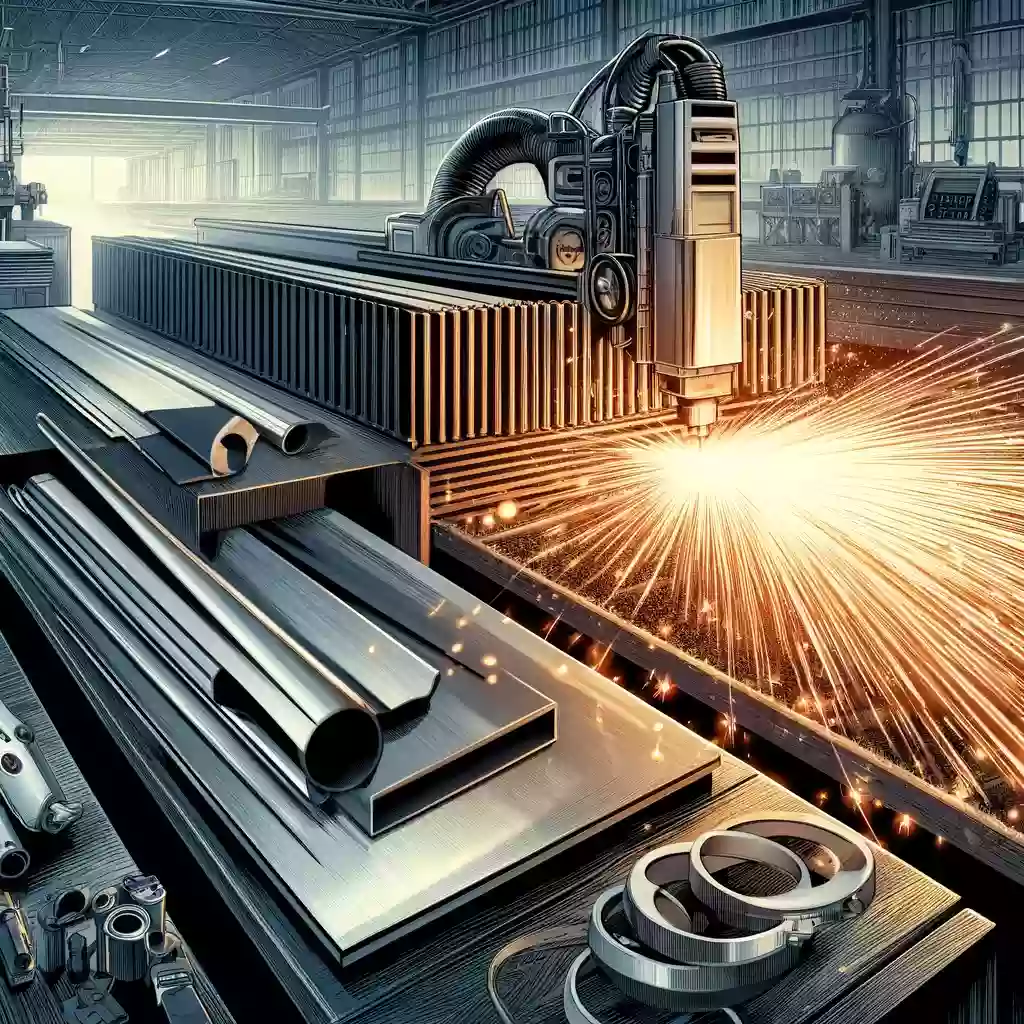
Fast cutting speed:
For materials with a thickness of no more than 2 cm, plasma cutting is faster than laser cutting.
2.Application restrictions:
Large heat-affected zone:
Since the temperature of plasma cutting is very high, the heat-affected zone is also large, which may affect the mechanical properties of the material.
Relatively low precision:
Plasma cutting is not as precise as laser cutting, and the cuts may require further processing.
Ⅳ.Comparison of application scenarios
1.Laser cutting machine:
Suitable for processing that requires high precision and complex graphics. Such as automobile manufacturing, aerospace, precision machinery, microelectronics manufacturing and other industries, especially where complex graphics and high-precision processing are required.
2.Wire cutting machine:
Mainly used for mold manufacturing, precision parts processing, etc., especially when processing materials that are difficult to process through traditional methods.
3.Plasma cutting machine:
Commonly used in shipbuilding, steel structure, heavy industry and other fields, suitable for quickly cutting large quantities of thick plate materials.
Ⅴ.Technology selection considerations
Factors to consider when choosing between these three cutting techniques include:
1.Material type and thickness:
Laser cutting is suitable for a variety of materials, wire cutting is mainly for carbide, etc., while plasma cutting is suitable for thick conductive materials.
2.Processing accuracy requirements:
If high-precision and complex graphics processing is required, laser cutting is the first choice. Wire cutting is suitable for processing carbide and complex small parts.
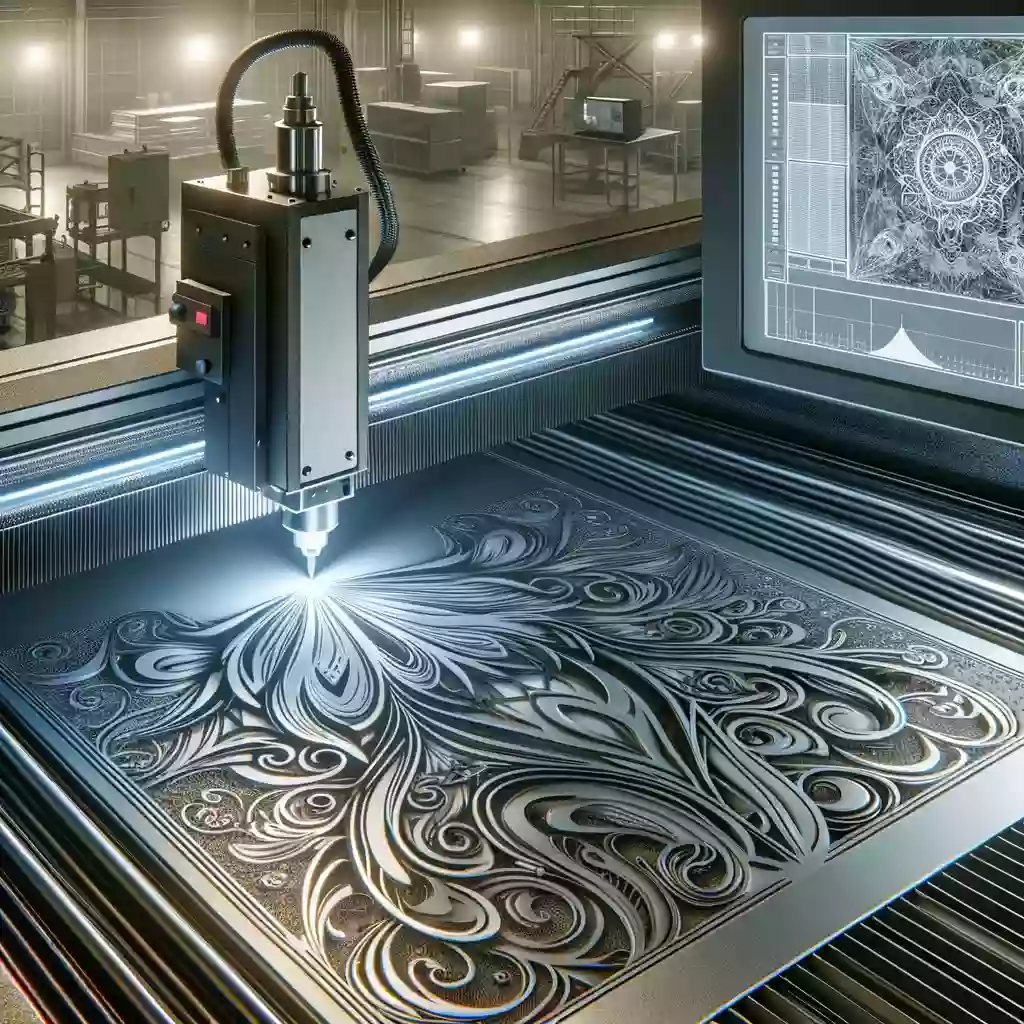
3.Production efficiency and cost:
Plasma cutting is low-cost and fast, making it suitable for mass production. Laser cutting is irreplaceable in some high-end applications because of its precision and flexibility, despite its higher cost.
Final Thoughts
Each cutting technology has its own unique advantages and limitations, and selecting the appropriate cutting technology requires a comprehensive judgment based on specific production needs, material characteristics and cost considerations. Understanding the core differences between these technologies can help manufacturing companies better optimize production processes and improve product quality.