In-depth Analysis of Laser Cutting Machine Cutting Precision
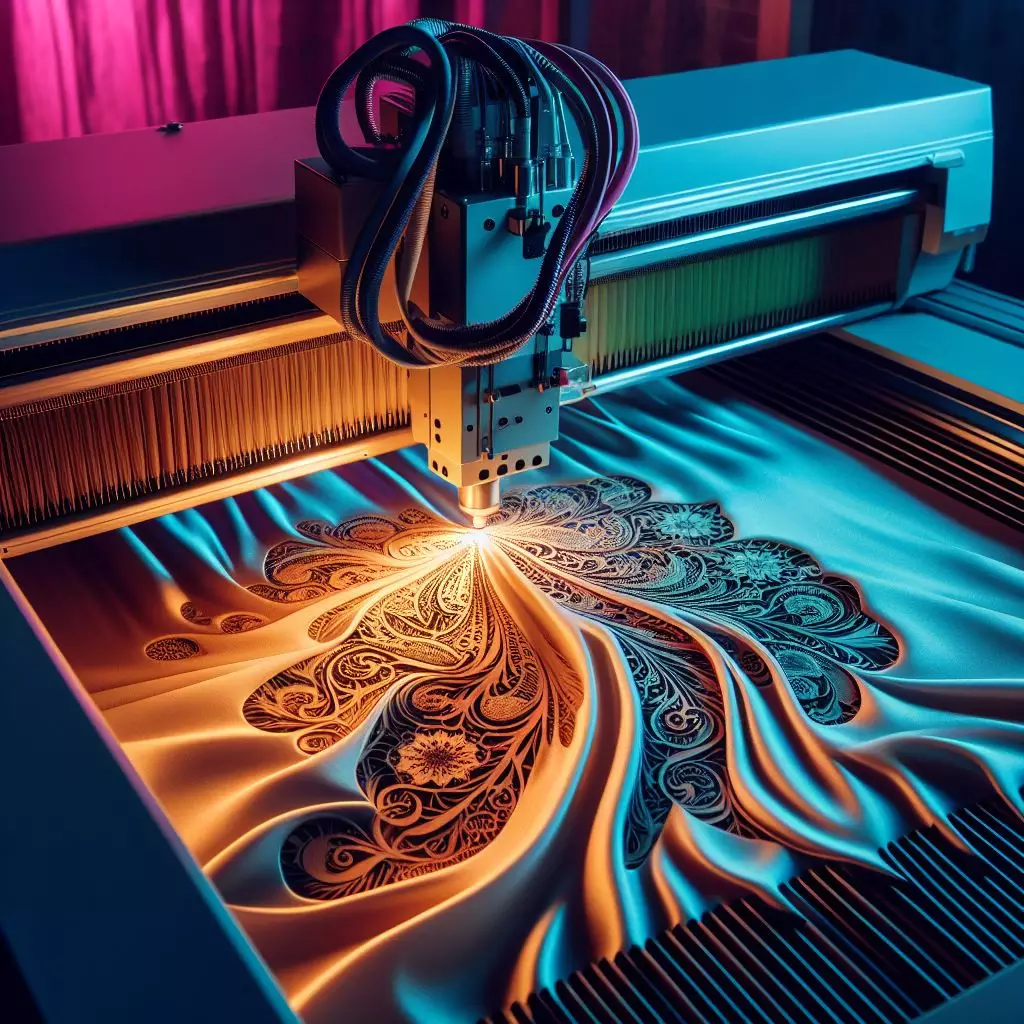
Laser cutting machines have revolutionized the manufacturing industry with their remarkable precision and versatility. However, achieving optimal cutting precision requires a thorough understanding of various factors that influence the process. This in-depth analysis explores the key elements affecting laser cutting machine cutting precision and strategies to enhance accuracy and consistency.
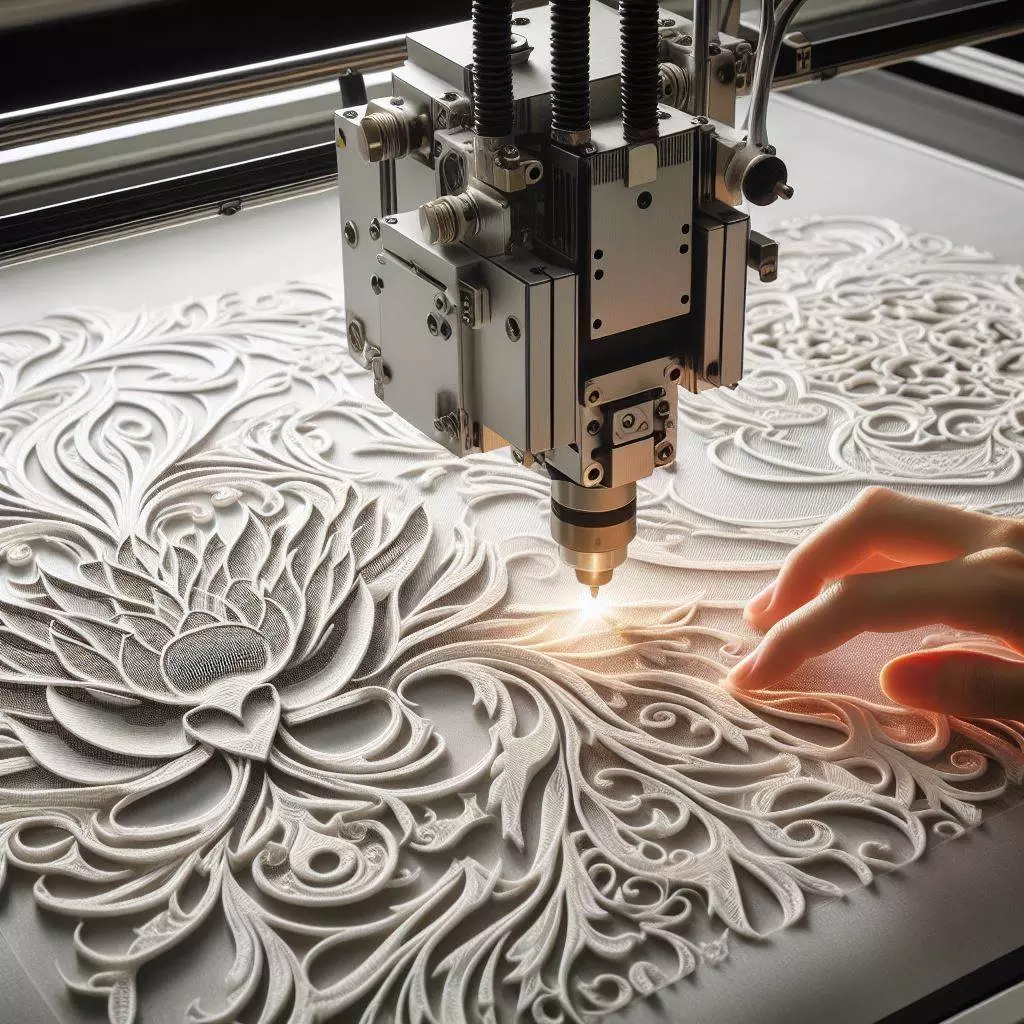
Understanding Laser Cutting Technology
Laser cutting technology utilizes a high-powered laser beam to melt, vaporize, or burn through materials, resulting in precise cuts. The process involves complex interactions between the laser beam, material properties, and machine parameters, ultimately influencing cutting precision.
Factors Affecting Cutting Precision
a. Material Properties: Different materials exhibit varying responses to laser cutting due to factors such as composition, thickness, and surface finish. Understanding material characteristics is crucial for adjusting cutting parameters to achieve optimal results.
b. Laser Beam Quality: The quality of the laser beam, including its focus, intensity, and stability, directly impacts cutting precision. High-quality laser systems produce consistent beam profiles, resulting in uniform cuts with minimal deviation.
c. Machine Dynamics: Mechanical factors such as machine rigidity, acceleration, and vibration control affect cutting precision. Stiff and stable machine structures minimize deflection and ensure accurate positioning of the laser beam.
d. Cutting Parameters: Parameters such as laser power, cutting speed, focal length, and assist gas pressure influence cutting precision. Fine-tuning these parameters based on material type and thickness is essential for achieving the desired cut quality.
e. Kerf Width: The width of the laser beam’s path, known as the kerf width, affects the accuracy of the cut. Optimizing the kerf width minimizes material loss and ensures precise cutting dimensions.
f. Edge Quality: Factors like beam focus, assist gas type, and nozzle design influence the quality of the cut edge. Smooth and clean edges indicate high cutting precision, while rough edges may require further processing.
Strategies to Enhance Cutting Precision
a. Calibration and Maintenance: Regular calibration and maintenance of laser cutting machines are essential for ensuring optimal performance and cutting precision. Periodic checks of machine components, optics, and alignment are crucial for minimizing errors.
b. Material Testing: Conducting material tests to determine the optimal cutting parameters for different materials improves cutting precision. Experimenting with varying laser settings helps identify the ideal parameters for achieving desired cut quality.
c. Advanced Control Systems: Implementing advanced control systems with real-time monitoring and feedback mechanisms enhances cutting precision. Closed-loop control systems adjust cutting parameters dynamically, compensating for variations in material properties and machine dynamics.
d. Beam Delivery Optimization: Optimizing beam delivery systems, including beam delivery optics and nozzle designs, improves cutting precision. Efficient beam delivery minimizes beam divergence and maintains consistent energy distribution across the cutting surface.
e. Process Monitoring: Incorporating process monitoring technologies such as laser power meters, beam profilers, and vision systems allows real-time monitoring of cutting performance. Detecting deviations from the desired cutting path enables immediate adjustments to maintain cutting precision.
f. Operator Training: Proper operator training on machine operation, material handling, and parameter adjustment is essential for achieving consistent cutting precision. Well-trained operators can identify and address issues that may affect cutting quality promptly.
Case Studies and Industry Examples
Explore case studies and examples from various industries showcasing the impact of cutting precision on product quality and manufacturing efficiency. Highlight successful implementations of cutting precision enhancement strategies and their results in real-world applications.
Conclusion
Laser cutting machine cutting precision is influenced by a multitude of factors, including material properties, laser beam quality, machine dynamics, cutting parameters, kerf width, and edge quality. By understanding these factors and implementing appropriate strategies, manufacturers can achieve high levels of cutting precision, resulting in superior product quality, reduced material waste, and enhanced manufacturing efficiency. Continued research and innovation in laser cutting technology will further advance cutting precision capabilities, driving the evolution of modern manufacturing processes.
In conclusion, achieving optimal cutting precision with laser cutting machines requires a comprehensive understanding of the factors influencing the process and implementing effective strategies to enhance accuracy and consistency. Through continuous refinement of technology and best practices, laser cutting remains at the forefront of precision manufacturing, enabling innovative solutions across various industries.