Selection of Gas and Pressure for Fiber Laser Cutting Machine
During the cutting process, fiber laser cutter needs to select appropriate cutting gas and gas pressure according to the material of different plates. These factors directly affect the cutting quality and efficiency. This article will discuss in detail the impact of cutting gas and its pressure on fiber laser cutting, and provide more detailed information.
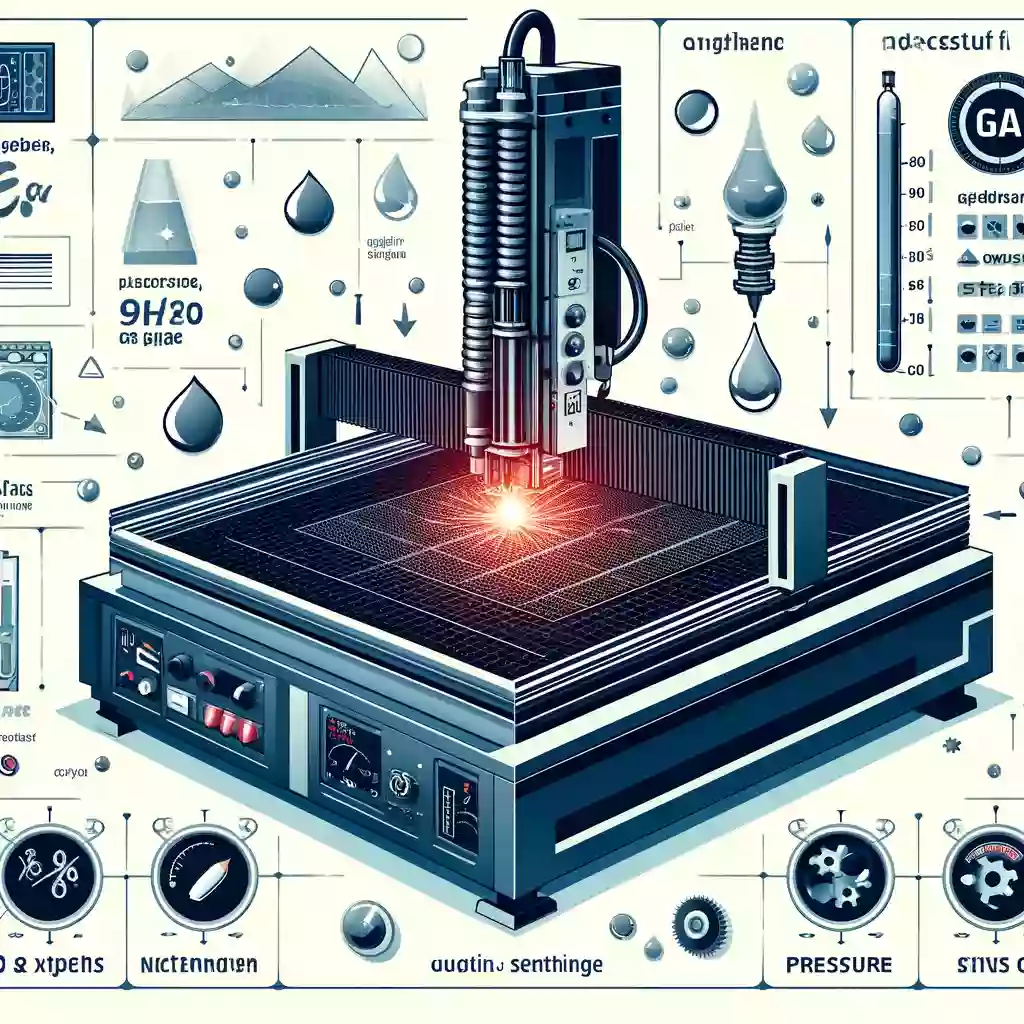
Ⅰ.Impact of Cutting Gas and Its Pressure on Cutting Quality
1. The role of cutting gas:
Cutting gas plays a vital role in the fiber laser cutting process. The main functions include heat dissipation, combustion support and blowing away slag, thereby improving cutting quality and efficiency. Commonly used cutting gases are oxygen, nitrogen and air.
2. Influence of insufficient gas pressure:
When the pressure of the cutting gas is insufficient, the following problems will occur:
Slag adhesion:
Insufficient pressure causes the slag to be unable to be effectively blown away, and it adheres to the cutting surface, affecting the cutting quality. These slags not only affect the appearance of the product, but may also affect subsequent processing steps.
Reduced cutting speed:
Insufficient gas pressure will lead to reduced cutting speed and fail to meet the requirements of production efficiency. Especially in large-scale production, the reduction in cutting speed will significantly affect the overall production progress and increase production costs.
3. Influence of excessive gas pressure:
When the pressure of the cutting gas is too high, it will have the following negative effects on the cutting quality:
Rough cutting surface:
Excessive pressure will make the cutting surface rough, the cutting slit will become wider, and the cutting accuracy will be affected. The rough cutting surface not only affects the product quality, but also may increase the difficulty of subsequent processing.
Section melting:
Excessive gas pressure may cause the cutting section to partially melt, and the ideal cutting section cannot be formed. This phenomenon is particularly obvious when cutting thick plates, and special attention should be paid.
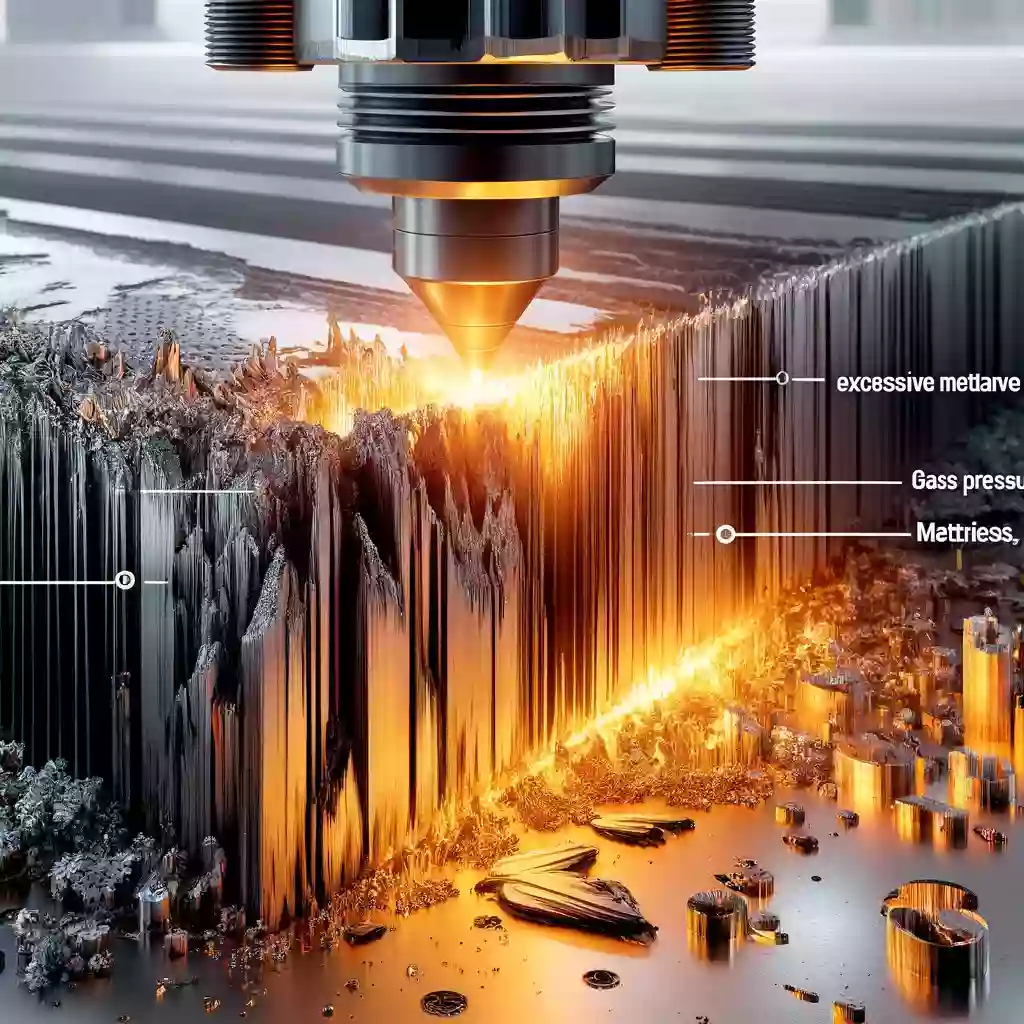
Ⅱ.The Effect of Cutting Gas Pressure on Perforation
1. The effect of too low gas pressure:
When the gas pressure is too low, the laser cannot effectively penetrate the cutting plate, resulting in longer perforation time and reduced production efficiency. Especially when processing thicker materials, low gas pressure will greatly weaken the penetration ability of the laser and increase the difficulty of perforation.
2. The effect of too high gas pressure:
When the gas pressure is too high, it will cause the melting of the perforation point and form a larger melting point, which will affect the cutting quality. High gas pressure will generate too much heat during the perforation process, causing the material to be over-melted locally, which is not conducive to fine cutting.
3. The effect of material thickness on gas pressure:
Cutting ordinary carbon steel:
As the thickness of the material increases, the pressure of the cutting gas needs to be reduced accordingly to avoid excessive slag and rough cutting surface. Lower gas pressure can reduce heat concentration and prevent excessive melting of the material.
Cutting stainless steel:
The pressure of the cutting gas usually increases with the thickness of the material to ensure cutting quality and efficiency. Higher gas pressure can increase the cutting speed of stainless steel and prevent oxidation of the cutting surface.
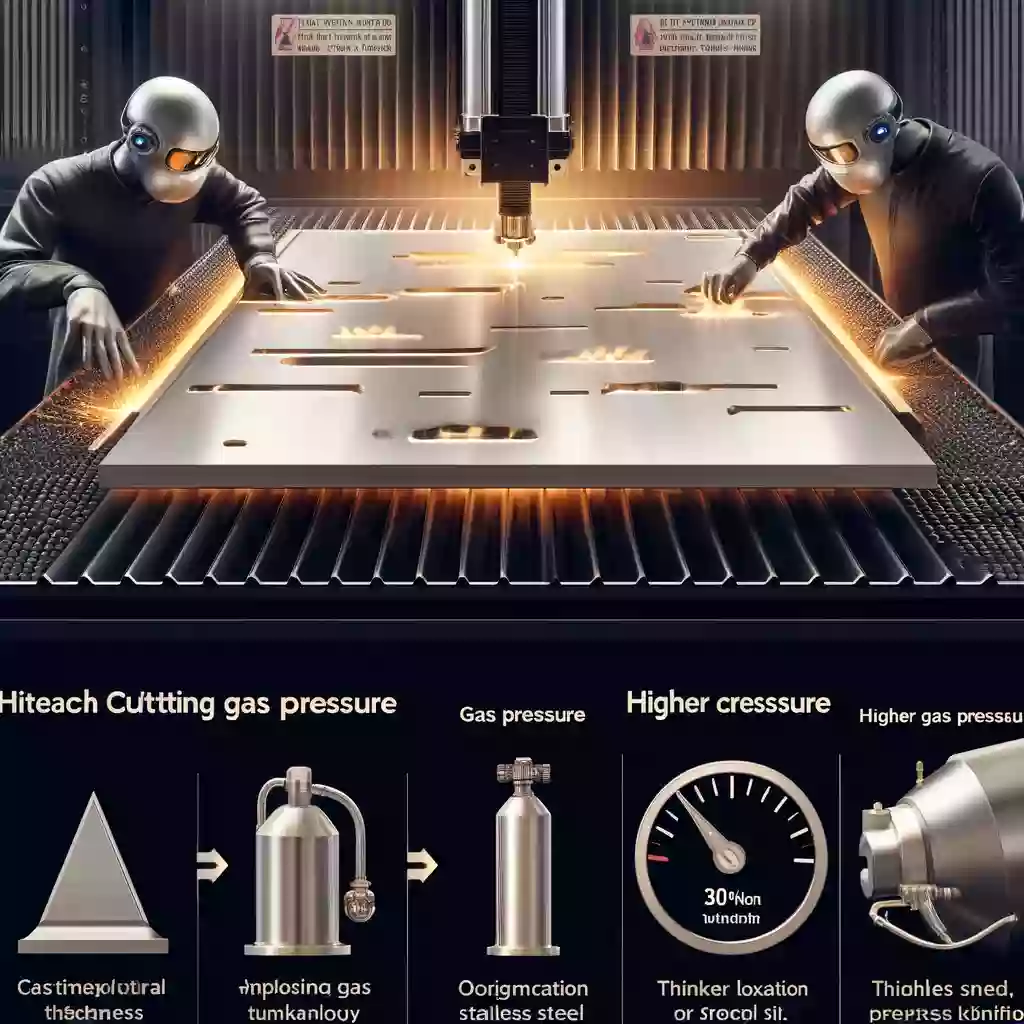
Ⅳ.Punching Strategies for Thin and Thick Plates
1. Punching thin plates:
Higher gas pressure is usually used to ensure fast perforation and cutting efficiency. Thin plate materials are easier to penetrate, and higher gas pressure can increase cutting speed and reduce processing time.
2. Punching thick plates:
Use a specific punching method combined with lower gas pressure to reduce damage to lenses and other cutting equipment. Thick plates require more laser energy and appropriate gas pressure to ensure punching quality and equipment life.
Ⅴ.Gas and Pressure Selection in Practical Applications
In practical applications, the selection of cutting gas and its pressure must be adjusted according to specific circumstances. Here are some common application examples and suggestions:
1. Thin plate cutting:
Choose a higher gas pressure, use nitrogen or oxygen, to ensure fast and high-quality cutting.
2. Thick plate cutting:
Choose moderate gas pressure, choose oxygen or nitrogen according to the material to ensure cutting quality and equipment protection.
3. Complex shape cutting:
It is necessary to finely control the gas pressure and cutting parameters, and choose the right gas to achieve the best results.
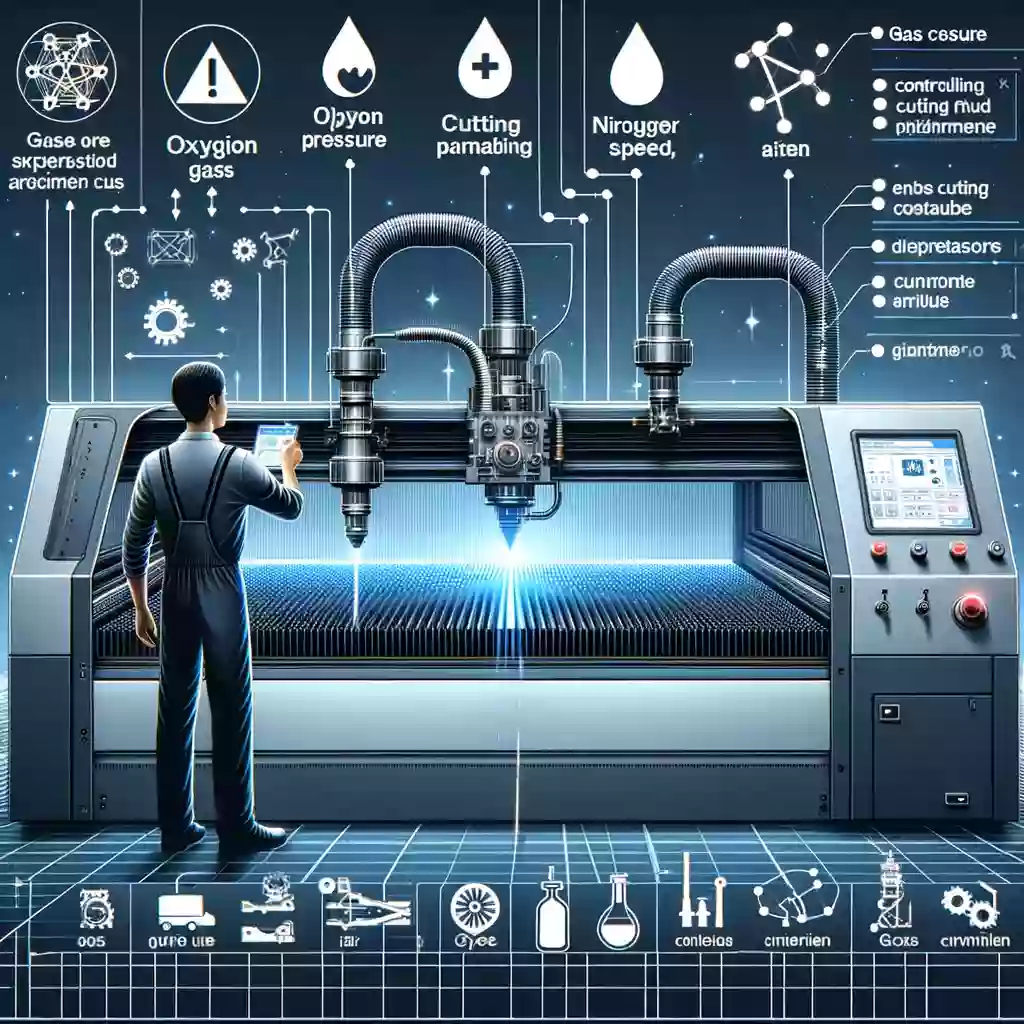
Final Thoughts
In short, the selection of cutting gas and its pressure during laser cutting must be flexibly adjusted according to actual conditions. Reasonable selection of cutting gas and control of its pressure can not only improve cutting quality and production efficiency, but also reduce operating costs and improve overall productivity. By continuously optimizing cutting processes and parameters, fiber laser cutters will play an increasingly important role in various industrial applications.