Application of Metal Laser Cutting Machines in Aerospace Material Processing
Metal laser cutting machines have revolutionized the aerospace manufacturing industry. As aerospace materials become increasingly complex and diverse, traditional cutting and machining methods struggle to meet the high precision and efficiency demands. Laser cutting technology, with its exceptional processing capabilities and accuracy, has emerged as a preferred solution for aerospace material processing. This blog will explore the principles of laser cutting, its applications in aerospace materials, and future trends in this transformative technology.
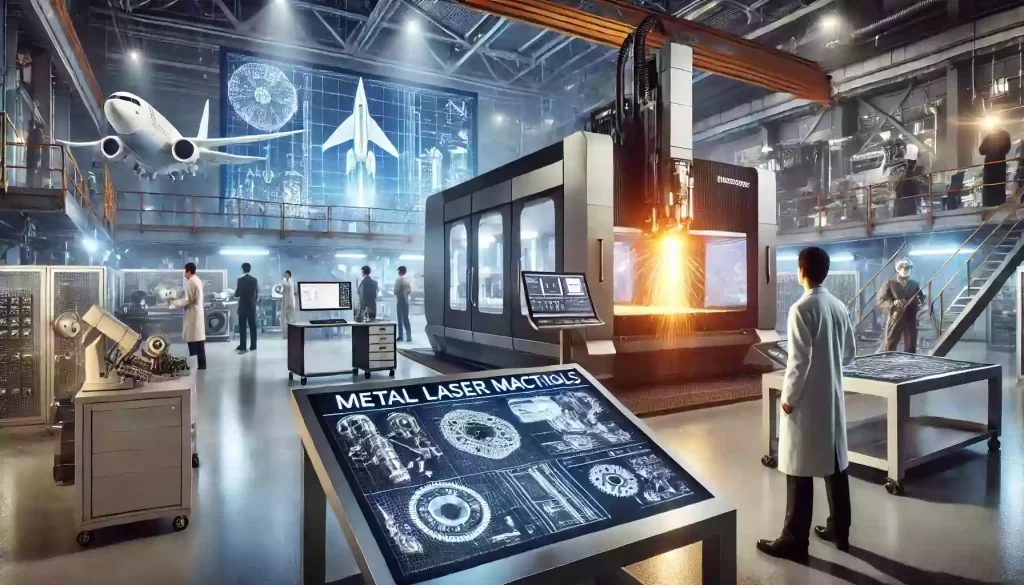
Ⅰ.How Laser Cutting Works
Fiber laser cutter uses a concentrated laser beam with high power density to irradiate the workpiece. This intense beam rapidly heats and melts the material at the focal point. By directing a high-speed jet of gas, usually oxygen or nitrogen, onto the molten area, the material is blown away, resulting in a precise cut. The laser cutting process involves three main components:
1.Laser source generation:
The laser beam is generated by a laser source, such as CO2, fiber, or Nd lasers.
2.Beam transmission and focusing:
The laser beam is transmitted through a series of mirrors or fiber optics and focused onto the material using lenses.
3.Material melting and removal:
The concentrated heat melts the material, and the assisting gas expels the molten material, forming a clean cut.
Ⅱ.Advantages of Laser Cutting
Fiber laser cutter offers several advantages over traditional mechanical cutting methods:
1.High precision:
Laser cutting achieves extremely high precision, ideal for intricate designs and tight tolerances required in aerospace materials.
2.High efficiency:
The process is swift, making it suitable for high-volume production environments.
3.Flexibility:
Capable of cutting various materials and thicknesses, laser cutting is versatile and adaptable.
4.Minimal heat-affected zone:
The narrow heat-affected zone reduces thermal distortion and maintains material integrity.
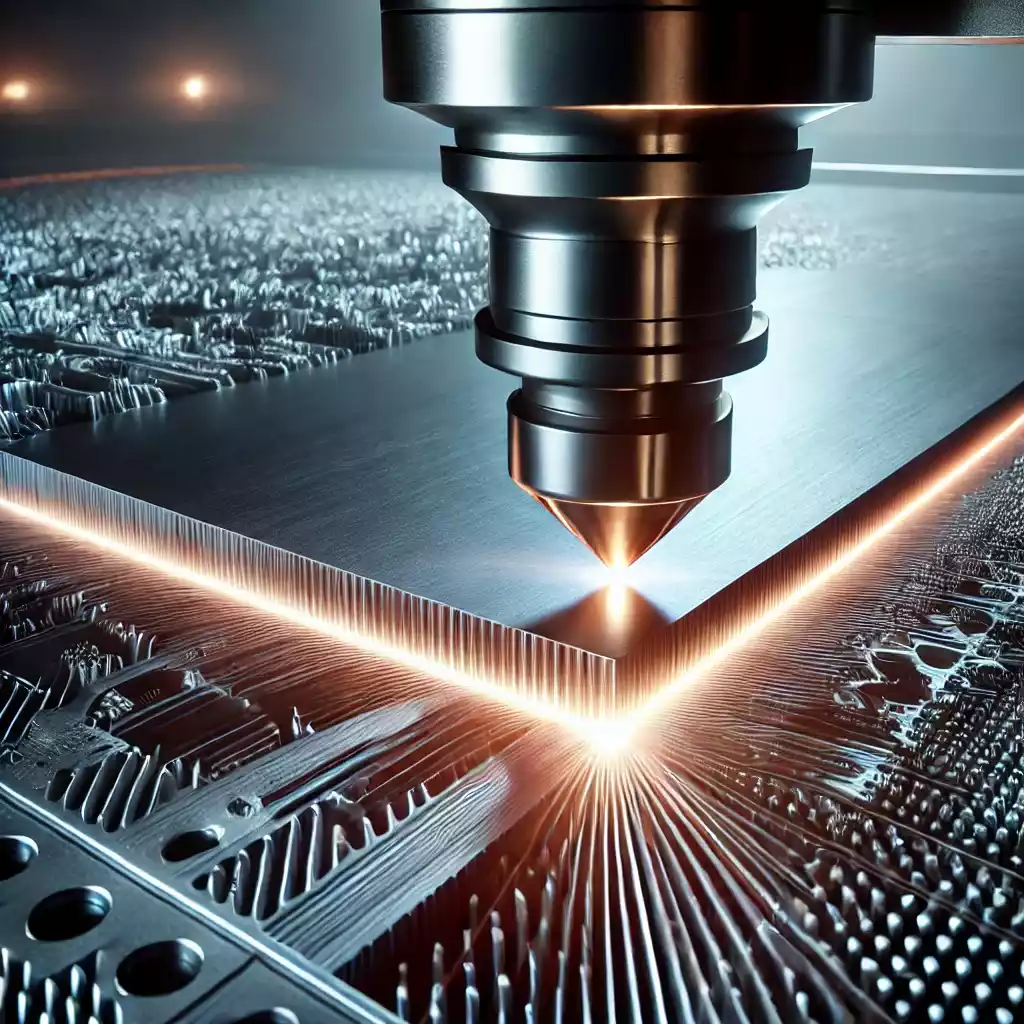
Ⅲ.Applications of Laser Cutting in Aerospace Material Processing
1.Common aerospace materials:
Aerospace manufacturing relies on a range of advanced materials to meet the demands of performance, durability, and weight reduction. Key materials include:
Aluminum Alloys:
Valued for their lightweight and high strength, used extensively in aircraft structures.
Titanium Alloys:
Known for their excellent strength-to-weight ratio and corrosion resistance, crucial for engine components and airframe structures.
Stainless Steel:
Provides durability and resistance to high temperatures and corrosion, commonly used for fuselage and internal components.
Composite Materials:
Such as carbon fiber composites, these materials combine light weight with high strength, increasingly used in modern aircraft.
2.Laser cutting of aluminum alloys:
Aluminum alloys are favored in aerospace for their combination of strength and low weight. However, their high reflectivity and thermal conductivity pose challenges in cutting. Advanced laser cutting machines overcome these challenges by adjusting the laser’s wavelength and focus, allowing precise and smooth cuts. This capability is essential for producing components with intricate shapes and tight tolerances.
3.Laser cutting of titanium alloys:
Titanium alloys are essential in aerospace due to their superior strength and corrosion resistance. The challenge in cutting titanium lies in its high melting point and reactivity. Laser cutting technology addresses this by using high-energy-density beams that quickly and efficiently cut through titanium, minimizing thermal effects and preserving the material’s properties.
4.Laser cutting of stainless steel:
Stainless steel is robust and resistant to corrosion, making it ideal for critical aerospace applications. Laser cutting stainless steel yields high precision and clean edges, crucial for both structural and aesthetic components. The non-contact nature of laser cutting ensures the surface integrity of the material remains intact, avoiding contamination or damage.
5.Laser cutting of composite materials:
Composite materials, especially carbon fiber composites, are increasingly used in aerospace for their high strength-to-weight ratio. Traditional cutting methods can cause delamination and damage. Laser cutting, with its precision and control, can cleanly cut these materials without compromising their structural integrity. This is particularly important for components where maintaining the fiber orientation and matrix integrity is critical.
Ⅳ.Trends in Laser Cutting Technology Development
1.Enhancing cutting efficiency and precision:
As laser technology advances, future laser cutting systems will offer even faster cutting speeds and higher precision. Innovations such as adaptive optics and real-time monitoring will further enhance the accuracy and efficiency of laser cutting, reducing processing time and costs while improving quality.
2.Smart and automated systems:
The integration of smart and automated systems into laser cutting machines is a key trend. Advanced sensors and control software enable machines to automatically adjust cutting parameters for different materials and thicknesses. This not only improves processing flexibility but also reduces the need for manual intervention, increasing throughput and consistency.
3.Adaptability to new materials:
With the continuous development of new aerospace materials, laser cutting technology must evolve to accommodate their unique properties. Future laser cutters will be designed to handle a broader range of materials, including next-generation composites and advanced alloys. This adaptability will be crucial for maintaining the cutting-edge capabilities required in aerospace manufacturing.
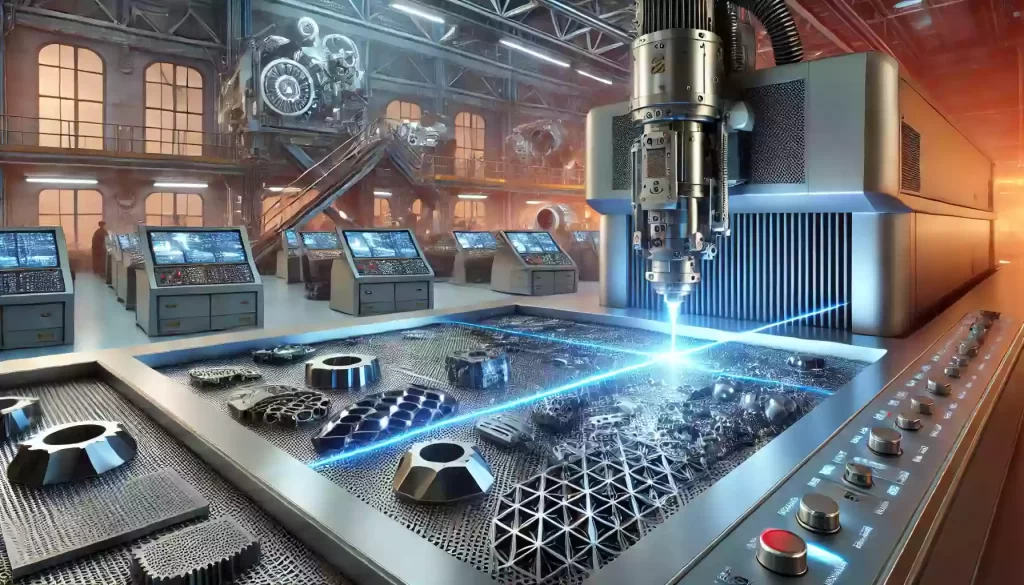
Final Thoughts
Metal laser cutting machines have significantly impacted the aerospace manufacturing industry by offering unparalleled precision, efficiency, and flexibility. As laser technology continues to evolve, its role in aerospace material processing will only become more prominent. From cutting lightweight aluminum alloys to handling advanced composites, laser cutting is paving the way for innovative aircraft designs and manufacturing processes.
By embracing and advancing laser cutting technology, the aerospace industry can look forward to enhanced productivity, improved product quality, and expanded possibilities in design and fabrication. The future of aerospace material processing will be shaped by the continued integration of laser cutting into the manufacturing landscape, driving the industry toward new heights of technological excellence.