Cleaning Principles and Measures for Fiber Laser Cutting Machines
Fiber laser cutters are vital tools in modern manufacturing, known for their efficiency and precise cutting capabilities. To maintain optimal performance, regular cleaning and maintenance are essential. This blog will explore the cleaning principles of fiber laser cutting machines, common cleaning measures, and how to effectively carry out daily maintenance to ensure long-term, stable operation of the equipment.
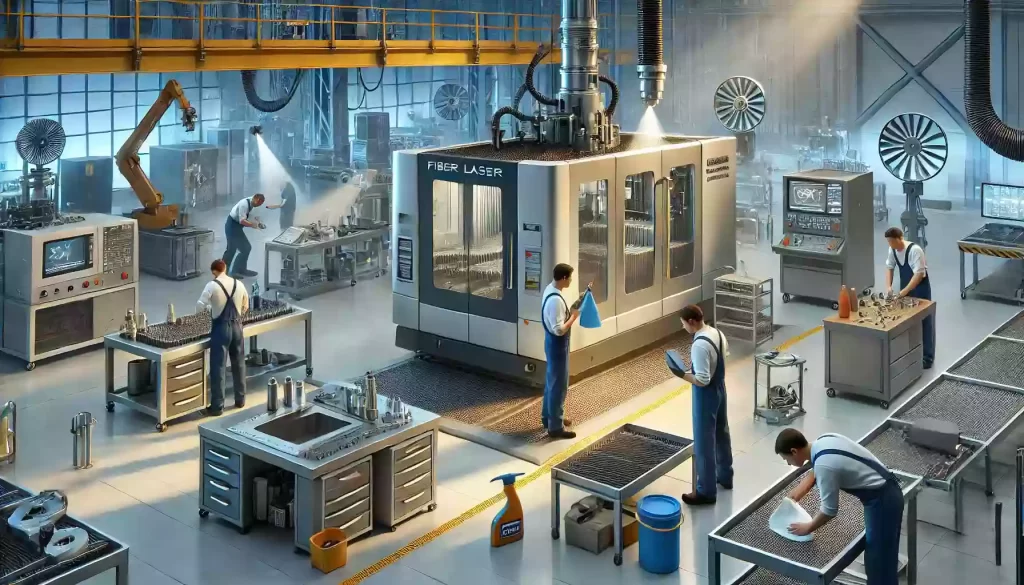
Ⅰ.Cleaning Principles of Fiber Laser Cutting Machines
1.Operating environment and cleaning requirements:
During the cutting process, fiber laser cutters generate a significant amount of smoke, metal debris, and other contaminants. If these pollutants are not promptly cleaned, they can accumulate on optical components, drive parts, and ventilation systems, affecting the machine’s efficiency and precision. Therefore, maintaining the cleanliness of a laser cutting machine is crucial not only for its normal operation but also for extending its service life.
2.Cleaning optical components:
Optical components are the core parts of a wood engraving machine, including the laser head, lenses, and mirrors. These components directly impact the quality of laser transmission and cutting performance. When dust or dirt accumulates on the surfaces of optical components, it can lead to energy loss and degradation of the laser beam quality. Therefore, cleaning optical components requires special care and precision.
3.Cleaning drive parts and rails:
The drive parts and rails are essential for ensuring the precise movement and positioning of the fiber laser cutting machine. Metal debris and dust generated during cutting can easily adhere to these parts, affecting their smooth operation and accuracy. Regular cleaning of the drive parts and rails can prevent wear and blockage, maintaining the stable operation of the equipment.
4.Cleaning the ventilation system:
The ventilation system is used to remove smoke and gases generated during cutting. If the ventilation system becomes clogged or filled with dust, it can reduce airflow efficiency, affecting cutting performance and the cleanliness of the working environment. Therefore, cleaning and maintaining the ventilation system is also a critical aspect of laser cutting machine upkeep.
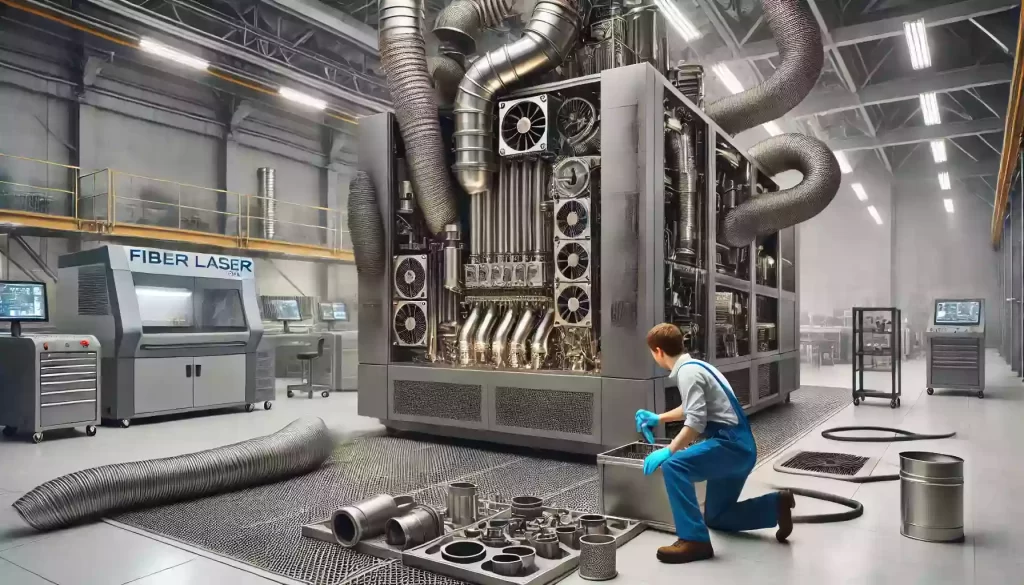
Ⅱ.Common Cleaning Measures
1.Methods for cleaning optical components:
Using Specialized Cleaners:
When cleaning optical components, use specialized optical cleaners or anhydrous ethanol. Avoid using ordinary cleaners to prevent chemical corrosion.
Soft Cleaning Tools:
Use soft cotton swabs or lint-free cloths to gently wipe the optical components, avoiding scratches on the surface caused by hard objects.
Regular Inspection and Cleaning:
Regularly inspect the cleanliness of optical components and determine the cleaning frequency based on usage. Typically, a weekly check is recommended, but it can be adjusted according to actual needs.
2.Methods for cleaning drive parts and rails:
Removing Surface Dust and Debris:
Use brushes or air blowers to remove dust and metal debris from the surfaces of the drive parts and rails.
Lubrication Maintenance:
After cleaning, apply an appropriate amount of lubricant to the drive parts and rails to ensure smooth operation.
Avoid Over-Cleaning:
Avoid using excessive cleaners or lubricants to prevent buildup and blockage.
3.Methods for cleaning the ventilation system:
Cleaning or Replacing Filters:
Regularly check the filters in the ventilation system and clean or replace any clogged filters to ensure smooth airflow.
Inspecting Exhaust Ducts:
Check the exhaust ducts for dust buildup or obstructions and clean out any contaminants from inside the ducts.
Maintaining Fans and Vents:
Ensure that fans and vents are not blocked or damaged, and regularly clean dust and dirt from fan blades.
Ⅲ.Effective Daily Maintenance Practices
1.Developing a cleaning and maintenance schedule:
To ensure the long-term stable operation of a fiber laser cutting machine, it is recommended to develop a detailed cleaning and maintenance schedule. Based on the frequency of use and working environment, determine the cleaning and maintenance intervals. For example, weekly inspection and cleaning of optical components, monthly cleaning of drive parts and rails, and quarterly maintenance of the ventilation system.
2.Training operators:
Operators are the first line of defense in daily maintenance. Provide training for operators on cleaning and maintenance procedures so they can correctly identify and address common contaminants and issues. Operators should be familiar with cleaning tools and methods and be able to promptly detect any anomalies during machine operation.
3.Using quality cleaning materials and tools:
Selecting appropriate cleaners, lubricants, and tools is crucial for ensuring cleaning effectiveness and equipment safety. Using high-quality cleaning materials can prevent damage to the equipment and improve the efficiency and effectiveness of cleaning.
4.Scheduling regular professional maintenance:
In addition to daily cleaning and maintenance, it is advisable to periodically invite professional technicians for comprehensive equipment inspections and maintenance. Professional maintenance can identify and resolve potential issues, preventing minor problems from developing into major faults.
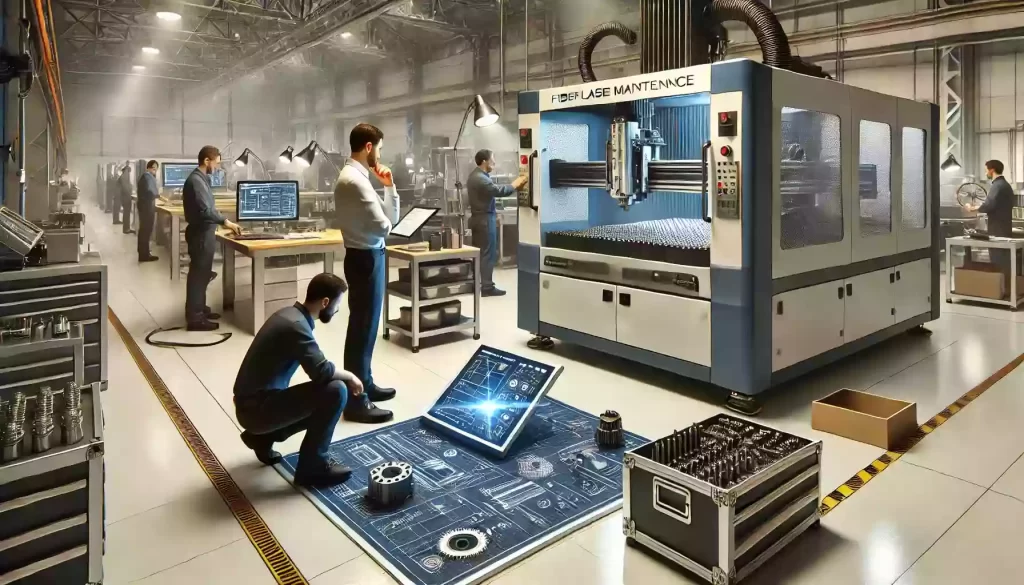
Final Thoughts
Cleaning and maintaining fiber laser cutting machines are essential for ensuring their efficient and stable operation. By understanding the basic principles of cleaning and taking effective cleaning measures, you can significantly extend the equipment’s service life and improve cutting quality. Whether it’s the optical components, drive parts, or ventilation system, all require careful maintenance and upkeep. By developing a detailed maintenance plan, training operators, and conducting regular professional maintenance, fiber laser cutting machines will continue to provide excellent performance, supporting the advancement of modern manufacturing.